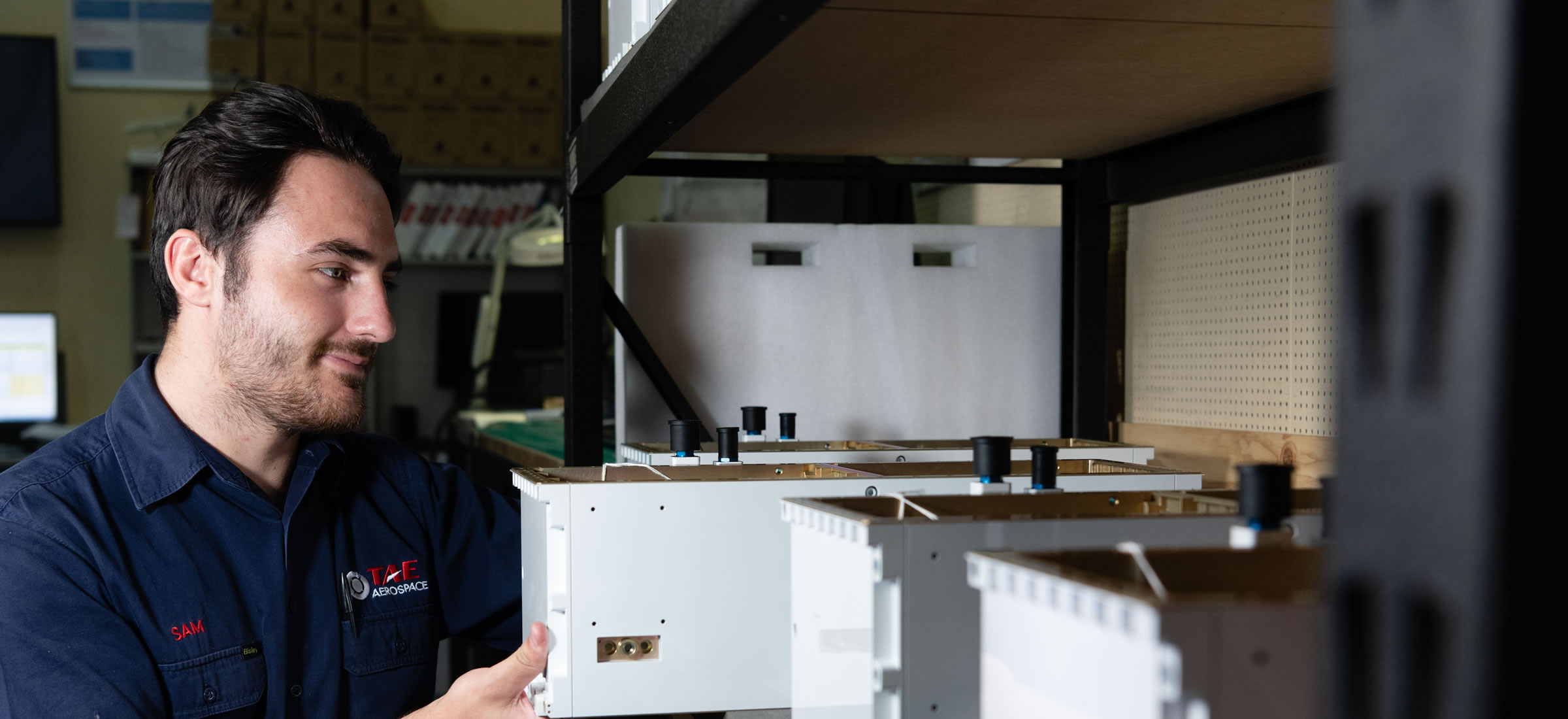
Advanced Manufacturing
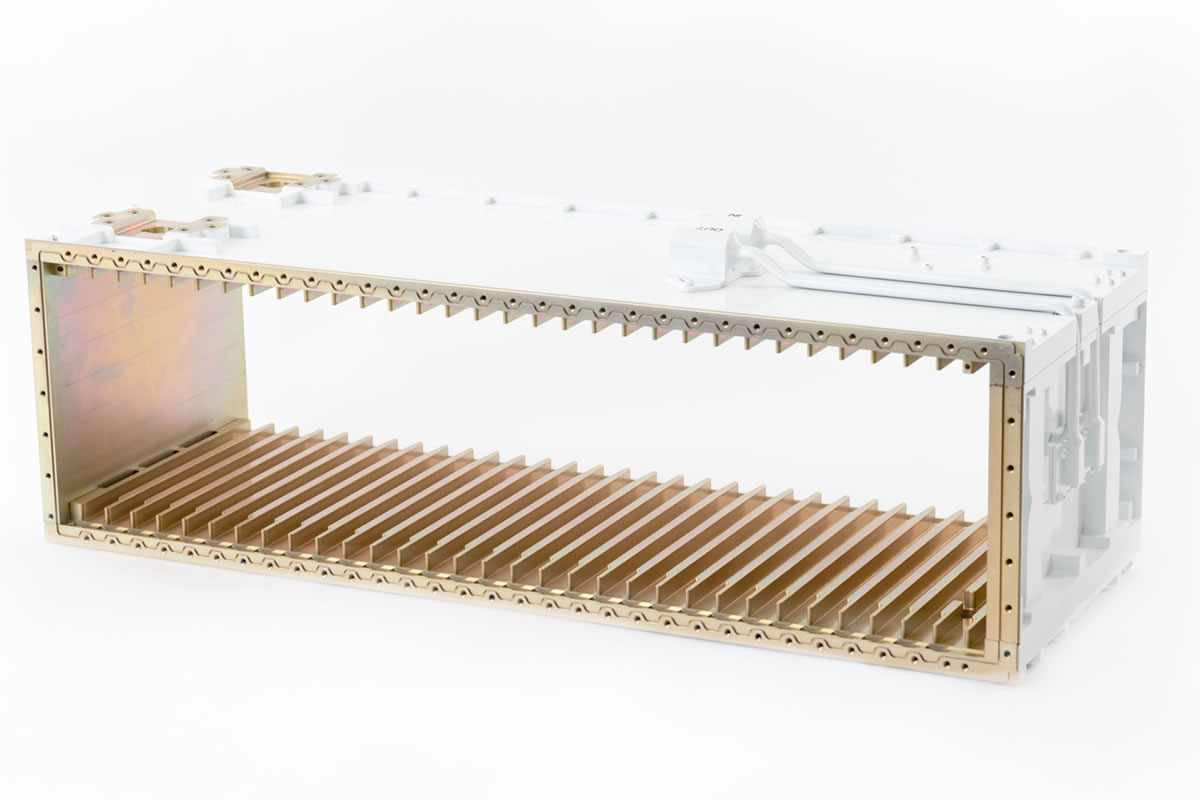
Aluminum vacuum brazing
Our niche aerospace manufacturing capability supports the manufacture of liquid-cooled components and enclosures for the global F-35 aircraft program.
Our core manufacturing process uses Aluminum Vacuum Brazing (AVB) technique, which is a process for fusing aluminum components to achieve:
- high-strength products that can operate at higher pressures and deliver leak-tight joints that allow integral liquid flow and electromagnetic interference reduction
- improved heat transfer and product stiffness (because micro channel fin stock can be included during the braze)
- reduced weight, compared with traditionally manufactured components
- lower component costs through reduced part counts and assembly labor
- excellent electrical and thermal conductivity, compared with an adhesive-bonded or mechanically-attached assembly
- improved product reliability
- greater design choice, especially for high performance products.
Currently, we provide several defense primes with:
- Cooled electronic/avionics enclosures including liquid-cooled chassis
- Cold plates
- Heat exchangers.
Between raw materials and fully completed components, our customers benefit from a complete, end-to-end solution in the brazing process: precision machining, heat treatment, conversion coating, painting, component assembly, proof-pressure testing and flow testing.

Aerospace manufacturing
Other specialist aerospace manufacturing capabilities we offer under our AS9100 Rev D approval:
- Computer controlled automatic shot peening
- Heat treatment, including for titanium
- Component painting
- Non-Destructive Testing (NDT)
- Extensive aerospace welding capability including high-strength super alloys and titanium components
Customers can also rely on us to inform the design and prototyping of components.